Composite Materials Die-Cutting Solutions
Tailored converting services for composite materials—designed for performance, precision, and production efficiency.
Composite Materials Die-Cutting
Provides advanced converting services for a wide variety of composite materials—including adhesive tapes, protective films, foam, fabric, and technical laminates. Our precision die-cutting, laminating, and slitting processes enable efficient production of custom parts for electronics, automotive, medical, and industrial applications.
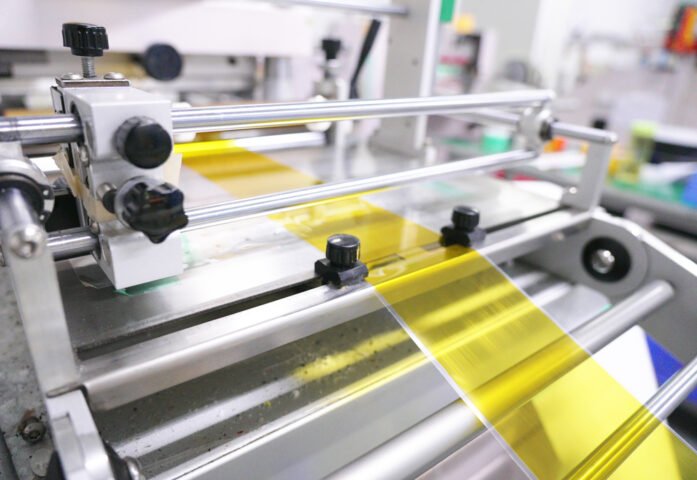
High-precision die-cutting
Advanced die-cutting equipment supports ±0.1mm or even higher precision, ensuring part consistency and fitting performance, meeting high standards such as electronics and medical.
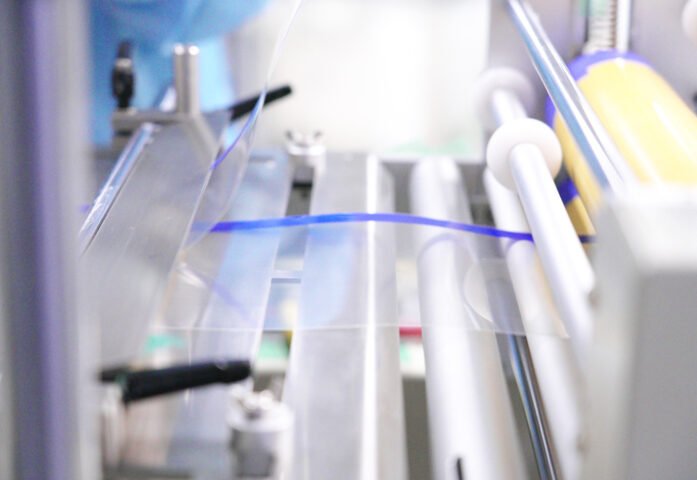
Strong material compatibility
Can handle a variety of flexible materials, including tapes, foam, PET/PI films, conductive/thermal conductive materials, non-woven fabrics, shielding materials, etc., suitable for different application scenarios.
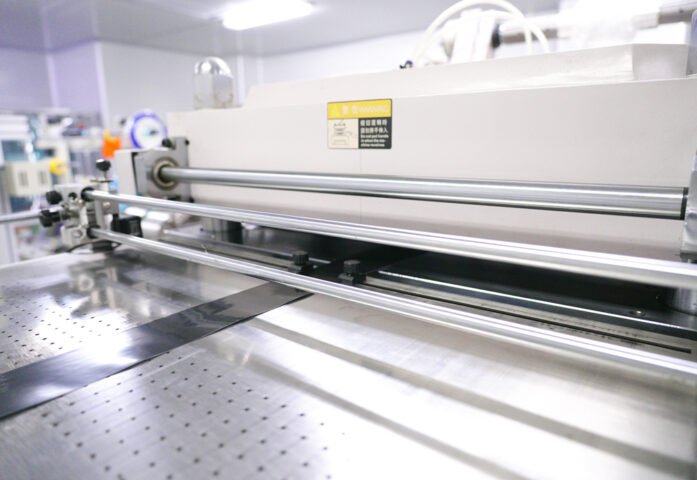
Multi-layer structure processing capabilities
Supports one-stop processing such as multi-layer composite, automatic lamination, back glue, and waste discharge, simplifying the customer assembly process and improving overall efficiency.
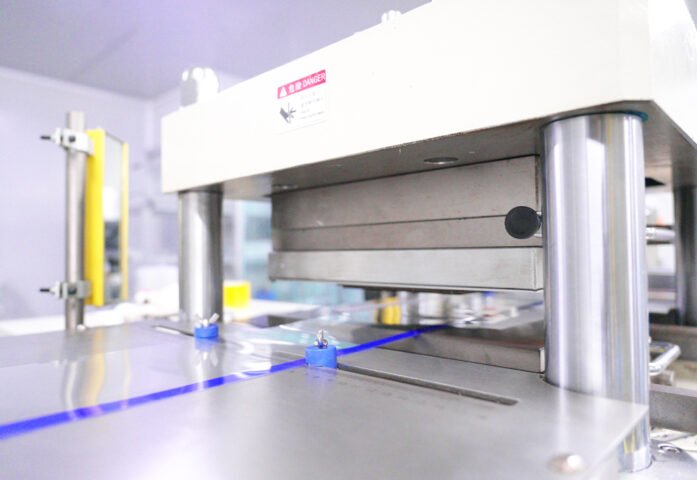
Clean environment guarantee
With Class 100~Class 1000 clean room die-cutting capabilities, it is suitable for industries with extremely high cleanliness requirements, such as medical, display modules, semiconductors, etc.
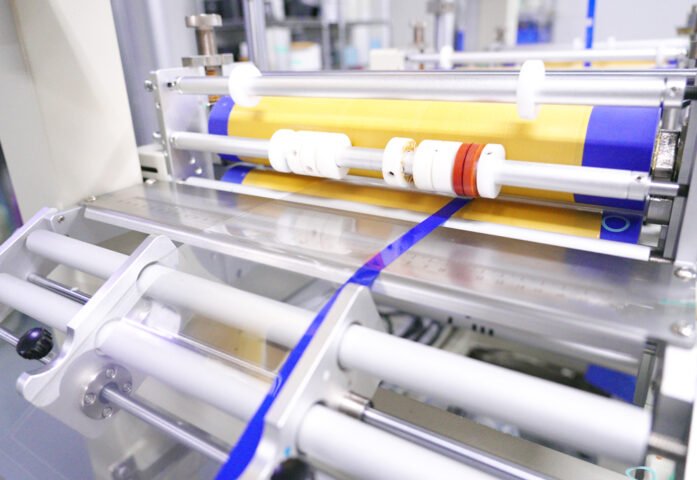
Fast proofing and flexible production
Quickly respond to customer customization needs, support from small batch proofing to large batch mass production, full process traceability management, and guaranteed delivery.
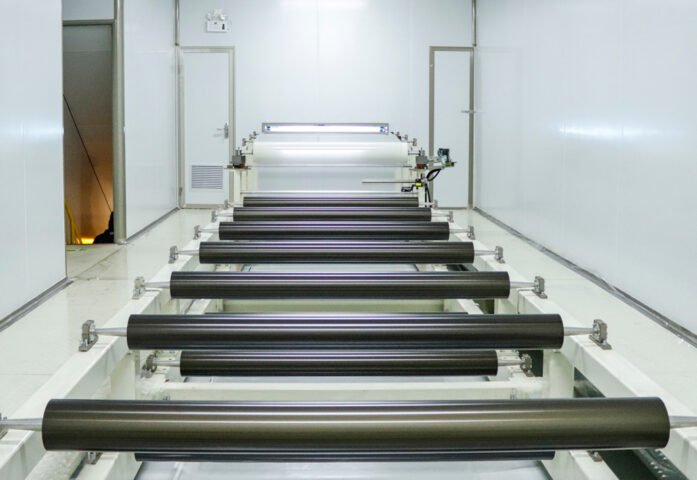
Applied in multiple industries
Widely serving high-end manufacturing fields such as consumer electronics, automobiles, new energy, medical equipment, optoelectronic displays, aerospace, etc.
What Is Composite Materials Converting
Composite materials converting refers to the process of transforming raw composite materials—such as adhesive tapes, films, foams, fabrics, and laminates—into precise shapes, parts, or components through specialized techniques like die-cutting, laminating, slitting cutting.
Why Composite Materials Converting Matters
The role of Composite Materials Converting is mainly reflected in processing raw composite materials into functional parts or structural parts that can be used in end products to meet the performance, shape and assembly requirements of specific industries.
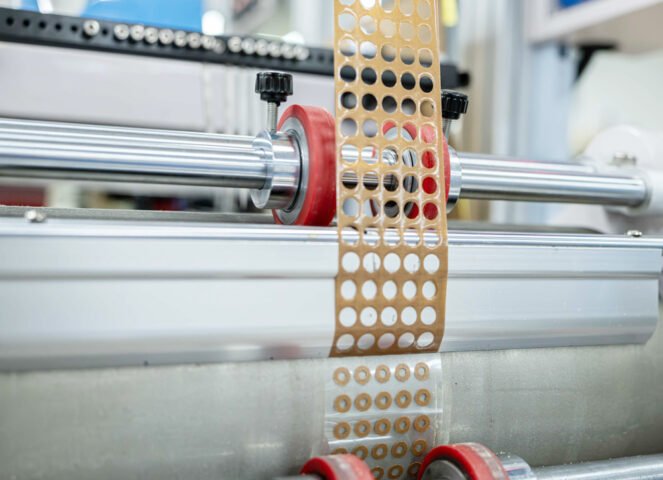
1. Composite materials converting transforms bulk rolls or sheets into ready-to-use parts with specific sizes, shapes, or formats — making them directly applicable in manufacturing or assembly.
2. By leveraging processes like die-cutting, laminating, slitting, and layering, converters can tailor composite materials to match the exact needs of a product’s design, including contours, perforations, and adhesive patterns.
3. By combining multiple materials — for example, thermal + insulation or waterproof + breathable layers — converting helps create multi-functional solutions like thermal pads, EMI shielding gaskets, or battery insulators.
4. Converted components are often delivered in roll-to-roll or sheet-to-sheet formats, which support automated or efficient manual assembly, saving time, reducing labor costs, and improving consistency.
5. Composite converting is highly flexible, supporting both prototyping for R&D and large-scale mass production — acting as a critical bridge between raw material suppliers and end-product manufacturers.
Industries & Applications
Yousan tape products and die-cutting solutions are widely used in multiple high-standard industries, meeting the multi-functional needs of bonding, fixing, sealing, insulation, buffering, thermal conductivity, etc. in different fields.
Frequently Asked Questions
Find quick answers to common questions about our adhesive tapes, die-cutting services, and customized solutions. We’ve compiled the most frequently asked inquiries from our clients to help you get the information you need—fast and efficiently.
We work with a wide range of materials including double-sided tapes, conductive films, optical films, thermal interface materials, foam, PET/PI, and more. Custom material sourcing is also available.
Industries such as electronics, automotive, medical devices, consumer products, new energy, aerospace, and display technologies all benefit from precise, application-ready components.
MOQ varies depending on the complexity, material type, and order size. We offer flexible volumes—from prototyping to full production runs.
Yes, we operate ISO-certified cleanrooms (Class 100 to Class 1000) to meet the strict cleanliness standards required by medical, optical, and semiconductor industries.
Simply contact our team with your drawings, specifications, or material requirements. We’ll evaluate the design, recommend materials if needed, and provide a quote and prototype timeline.
Yes. Our application engineers can recommend suitable materials based on your product’s functional needs—such as adhesion, insulation, thermal management, EMI shielding, or optical clarity.
We accept most common CAD formats, including DXF, DWG, AI, and PDF. If needed, we can also assist with file conversion or drawing adjustments.
Let’s Connect with Yousan
Contact our team for one-on-one technical support and tailored adhesive tape solutions.